Täppismetallist detaile valmistatakse sageli mitmesuguste täppistöötlustehnoloogiate abil, kusjuures CNC-töötlus on levinud meetod. Tavaliselt nõuavad täppisdetailid nii mõõtmete kui ka välimuse osas kõrgeid standardeid.
Seetõttu on CNC-töötlemisel metallide, näiteks alumiiniumi ja vase puhul probleemiks tööriistajälgede ja -joonte teke valmistoote pinnal. Selles artiklis käsitletakse tööriistajälgede ja -joonte tekkimise põhjuseid metalltoodete töötlemisel. Pakume välja ka võimalikke lahendusi.
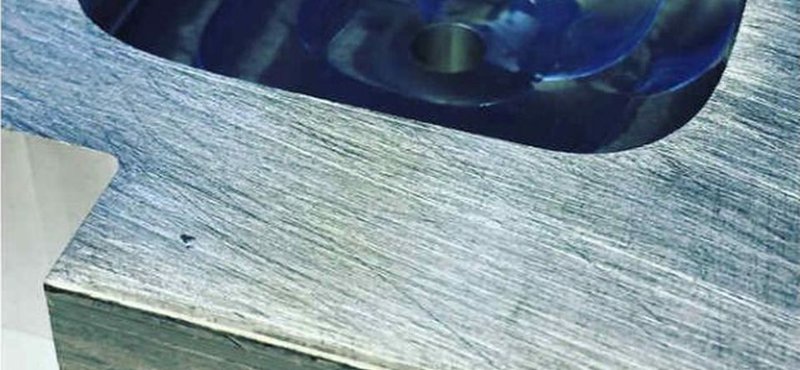
Kinnitusvahendite ebapiisav kinnitusjõud
Põhjused:Mõned õõnsustega metalltooted vajavad vaakumkinnitusi ja neil võib olla raskusi piisava imemisjõu tekitamisega pinna ebatasasuste tõttu, mille tulemuseks on tööriistajäljed või jooned.
Lahendus:Selle leevendamiseks kaaluge üleminekut lihtsalt vaakumimemiselt vaakumimemisele koos rõhu või külgtoega. Teise võimalusena uurige alternatiivseid kinnitusvõimalusi, mis põhinevad konkreetsetel detailide struktuuridel, kohandades lahendust konkreetsele probleemile.
Protsessiga seotud tegurid
Põhjused:Probleemi võivad põhjustada teatud tootmisprotsessid. Näiteks tahvelarvutite tagakorpuste töötlemisetapid hõlmavad külgmiste aukude stantsimist ja seejärel servade CNC-freesimist. See jada võib kaasa tuua märgatavaid tööriistajälgi, kui freesimine jõuab külgmiste aukude asendisse.
Lahendus:Selle probleemi tavaline näide tekib siis, kui elektroonikaseadmete kestade jaoks valitakse alumiiniumisulam. Selle lahendamiseks saab protsessi muuta, asendades külgmiste aukude stantsimise ja freesimise ainult CNC-freesimisega. Samal ajal tagades tööriista ühtlase haardumise ja vähendades freesimisel ebaühtlast lõikamist.
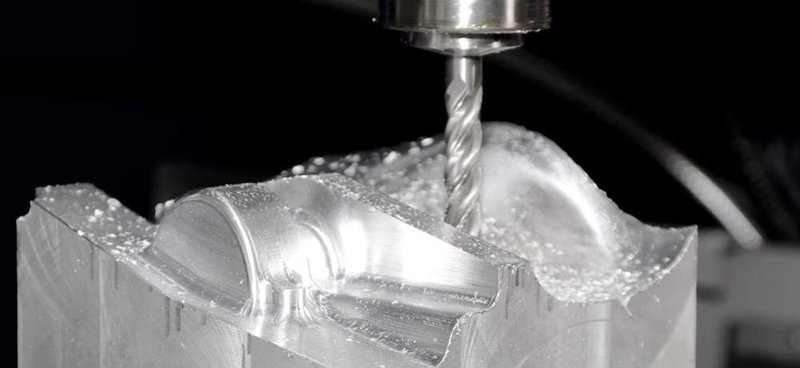
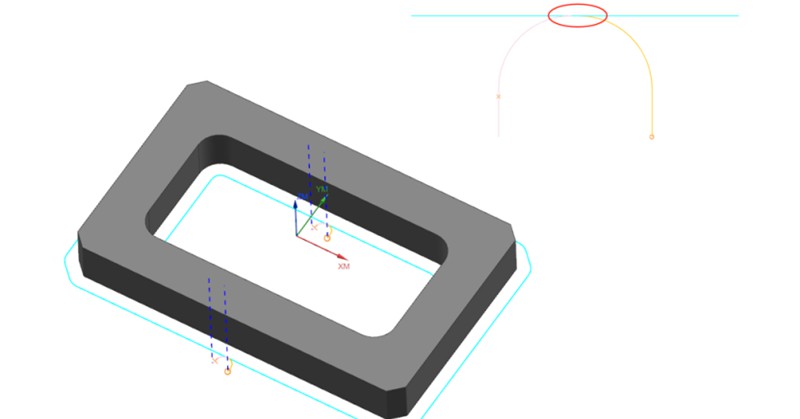
Tööriista raja ebapiisav programmeerimine
Põhjused:See probleem tekib tavaliselt toote tootmise 2D-kontuurtöötluse etapis. CNC-programmis on halvasti kavandatud tööriistatee haardumine, mis jätab jälgi tööriista sisenemis- ja väljumispunktidesse.
Lahendus:Tööriistajälgede vältimise probleemi lahendamiseks sisenemis- ja väljumispunktides hõlmab tüüpiline lähenemisviis tööriista haakumiskauguse kerge kattumise (umbes 0,2 mm) sisseviimist. See tehnika aitab vältida masina juhtkruvi täpsuse võimalikke ebatäpsusi.
Kuigi see strateegia hoiab ära tööriistajälgede tekkimise, põhjustab see pehmest metallist toote puhul korduvat töötlemist. Seetõttu võib sellel lõigul olla tekstuuri ja värvi erinevusi võrreldes teiste piirkondadega.
Kalasooma mustrid tasastel töödeldud pindadel
Põhjused:Toote tasasel pinnal esinevad kalasoomused või ringikujulised mustrid. Pehmete metallide, näiteks alumiiniumi/vase töötlemiseks kasutatavad lõikeriistad on üldiselt 3–4 soonega sulammaterjalide freesid. Nende kõvadus on vahemikus HRC55 kuni HRC65. Need freesimisriistad töödeldakse tööriista alumist serva ja detaili pinnale võivad tekkida iseloomulikud kalasoomuse mustrid, mis mõjutavad selle üldist välimust.
Lahendus:Tavaliselt täheldatakse seda toodete puhul, millel on kõrged tasasusnõuded ja süvistatud struktuuridega tasaste pindade puhul. Lahenduseks on üleminek sünteetilisest teemantmaterjalist lõikeriistadele, mis aitavad saavutada siledama pinnaviimistluse.
Seadmete komponentide vananemine ja kulumine
Põhjused:Toote pinnal olevad tööriistajäljed on tingitud seadme spindli, laagrite ja juhtkruvi vananemisest ja kulumisest. Lisaks aitavad ebapiisavad CNC-süsteemi lõtkuparameetrid kaasa märgatavatele tööriistajälgedele, eriti ümarate nurkade töötlemisel.
Lahendus:Need probleemid tulenevad seadmetega seotud teguritest ja neid saab lahendada sihipärase hoolduse ja asendamisega.
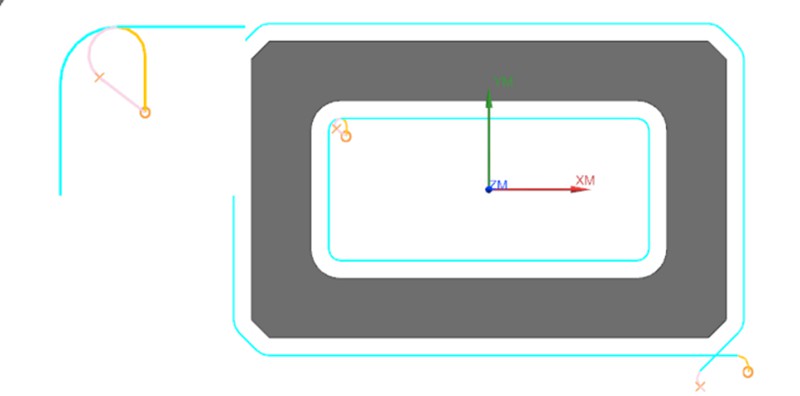
Kokkuvõte
CNC-töötlemismetallide ideaalse pinna saavutamiseks on vaja kasulikke lähenemisviise. Tööriistajälgede ja -joonte vältimiseks on erinevaid meetodeid, mis hõlmavad seadmete hoolduse, kinnitusdetailide täiustamise, protsesside kohandamise ja programmeerimise täiustamise kombinatsiooni. Nende tegurite mõistmise ja parandamise abil saavad tootjad tagada, et täppiskomponendid mitte ainult ei vasta mõõtmetele, vaid omavad ka soovitud esteetilisi omadusi.